Mark Bignell
Director
Specialising in Aerospace, Automotive, Commercial Vehicle, EV, Manufacturing, Motorsport
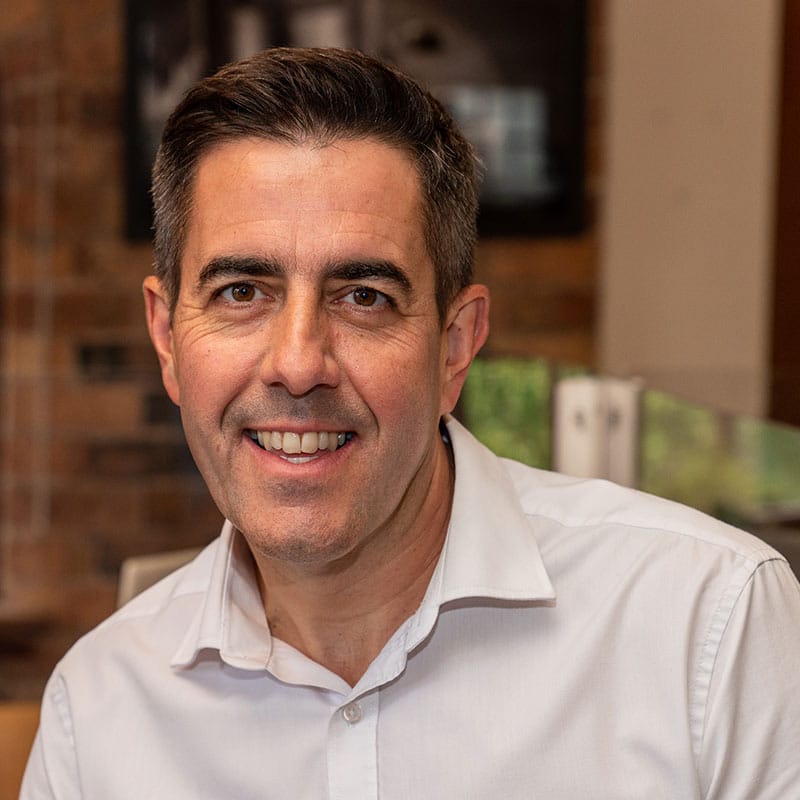
​About Mark
Away from work
I love keeping fit, socialising and especially watching my two daughters growing up and starting to answer Daddy back!!
​I’m skilled in recruiting for the following positions / sectors:
Product Development & Advanced Technology – Product Engineer, Design Engineer, Senior Design Engineer, Development Engineer, Electrical Engineer, Mechanical Engineer, Senior Engineer, Lead Engineer, Principal Engineer, Chief Engineer, Design Manager, Engineering Manager, Engineering Director, Programme/Project Manager, Programme/Project Director
Manufacturing & Operations – Manufacturing Engineer/Manager, Production Engineer/Manager, Process Engineer/Manager, Quality Engineer/Manager, Applications Engineer, Project Engineer/Manager, Engineering Manager/Director, Operations Manager/Director, General Manager