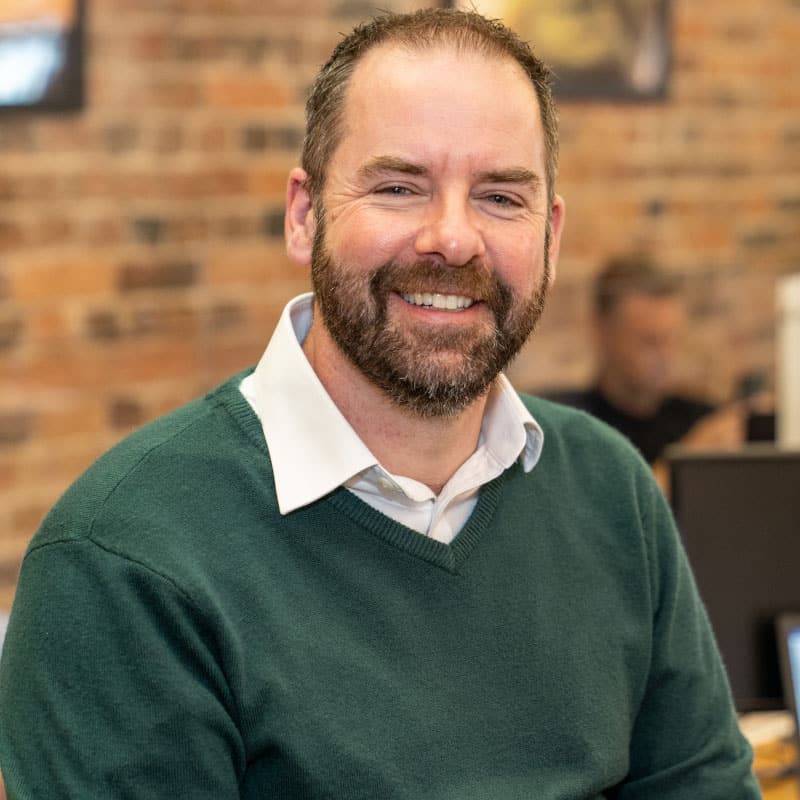
​About Dan
Away from work
My 3 children keep me busy, but I love the coast, North Devon and North Wales in particular, spending quality time with friends and family is important. Interesting fact: I sailed across the Atlantic when I was 19.
I enjoy music, especially festivals and the first Glastonbury I went to was in 1994!
​Areas I specialise in:
Operational Management, to include supply chain, purchasing, logistics, general management, but I’ve been around the block a bit, so I can turn my hand to many different jobs.